Innovative Fads in Steel Manufacture: Enhancing Toughness and Precision
In the realm of steel construction, the quest of toughness and accuracy has actually led to a wave of ingenious patterns that are improving the market. From advancements in welding modern technologies to the assimilation of robot automation in manufacture procedures, the landscape of steel production is developing quickly. High-strength alloy growth, paired with the application of 3D modeling and simulation software program, is pressing the borders of what is possible in regards to structural stability and accuracy. The growing emphasis on lasting methods in steel production is not only driving effectiveness but additionally promoting a more eco conscious strategy to manufacture. These patterns are not just forming the present but likewise preparing for the future of steel manufacture, guaranteeing additional improvements in sturdiness and precision.
Advanced Welding Technologies
In the realm of steel fabrication, the fostering of advanced welding innovations has dramatically reinvented the industry's technique to accomplishing remarkable top quality and accuracy in structural welds. Advanced welding modern technologies, such as laser beam welding and friction mix welding, have arised as game-changers in the area. By leveraging these sophisticated welding strategies, steel fabricators can elevate the durability, stamina, and precision of their structural welds, satisfying the progressively demanding requirements of modern building and construction tasks.
Robot Automation in Construction
Accepting robot automation has actually come to be a cornerstone of contemporary steel construction practices, improving and improving processes performance throughout the market. Robots are reinventing the means steel elements are produced, offering unparalleled accuracy and speed while minimizing human error. These automated systems can deal with repeated tasks with regular precision, bring about greater top quality final product.
One secret benefit of robot automation in steel construction is the capacity to function around the clock without fatigue, significantly enhancing manufacturing output. This continual operation decreases downtime and speeds up project timelines, eventually conserving prices for manufacturers. Additionally, robots can be programmed to execute intricate tasks that might be challenging or hazardous for human workers, boosting security in the workplace.
In addition, robot automation makes it possible for seamless integration with other digital modern technologies, such as computer-aided style (CAD) software program and Internet of Points (IoT) systems (steel fabrication melbourne). This interconnected approach boosts communication in between different stages of construction, optimizing workflows and making sure real-time tracking and control. As the steel construction market remains to develop, robotic automation stands out as a transformative force driving efficiency and accuracy in manufacturing procedures

High-Strength Alloy Growth
The improvement of high-strength alloy advancement in steel fabrication is reshaping the sector's strategy to improving product sturdiness and performance. High-strength alloys are crafted to show remarkable mechanical buildings, such as boosted tensile stamina, strength, and corrosion resistance contrasted to conventional steel grades. By you could try these out incorporating these sophisticated alloys into fabrication procedures, makers can create components that stand up to higher stress and anxiety levels and rough atmospheres, causing more trustworthy and resilient output.
One key benefit of high-strength alloy development is the capability to decrease product thickness without endangering structural integrity. This not just results in lighter-weight elements but likewise adds to cost financial savings and improved effectiveness in fabrication and setting up procedures. The enhanced strength-to-weight ratio of these alloys enables for the layout and building and construction of structures with higher load-bearing capabilities while decreasing general weight.
3D Modeling and Simulation Software Application
Improvements in steel fabrication processes have actually been significantly pushed by the assimilation of advanced 3D modeling and simulation software devices. These tools allow makers to create detailed online versions of their jobs, enabling them to imagine the final product with precision before any type of physical job begins.
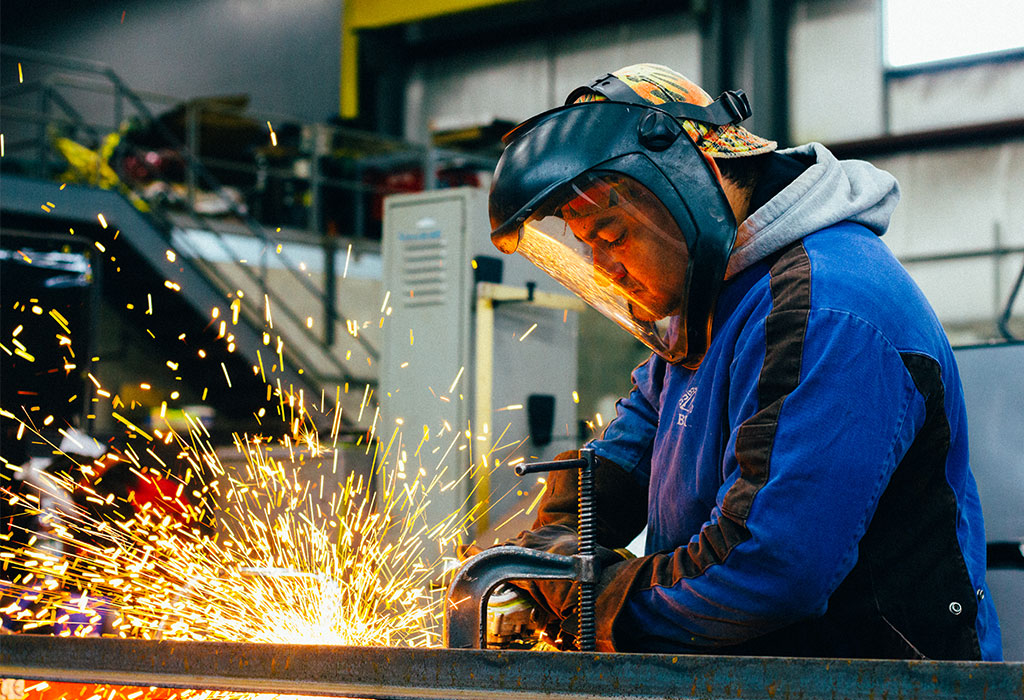
Sustainable Practices in Steel Manufacturing
Integrating sustainable methods right into steel production processes is crucial for lessening ecological influence and guaranteeing lasting source schedule. One vital lasting method is the adoption of energy-efficient modern technologies to lower greenhouse gas discharges during the steel production procedure. This includes making use of renewable resource resources, such as solar or wind power, to power steel plants and executing energy-efficient tools to enhance power usage.
An additional crucial element of lasting steel manufacturing is the accountable sourcing of raw products. This entails guaranteeing that the iron ore and various other resources utilized in steelmaking are acquired from eco pleasant and moral resources. By advertising openness in the supply chain and sticking to rigorous environmental requirements, steel makers can minimize the unfavorable impacts of resource removal on local environments and areas.

Verdict
To conclude, the cutting-edge trends in steel fabrication such as sophisticated welding technologies, robot automation, high-strength alloy development, 3D modeling and simulation software application, and sustainable methods are boosting the sturdiness and precision of steel items. These advancements are revolutionizing the steel manufacture industry by enhancing sustainability, effectiveness, and high quality. It is clear that the future of steel manufacture depends on accepting these sophisticated technologies to fulfill the demands of contemporary building and construction and production industries.
In the realm of steel fabrication, the pursuit of sturdiness and precision has actually led to a wave of cutting-edge trends that are improving the market.In the world of steel fabrication, the adoption of cutting-edge welding modern technologies has actually substantially transformed the market's technique to achieving premium high quality and precision moved here in architectural welds. As the steel construction industry continues to evolve, robotic automation stands out as a transformative force driving performance and precision in producing procedures.
Additionally, recycling and reusing steel scrap and waste materials play a substantial function in enhancing the sustainability of steel manufacturing. metal fabrication melbourne.In final thought, the innovative fads in steel construction such as innovative welding innovations, robot automation, high-strength alloy advancement, 3D modeling and simulation software, and lasting methods are boosting the sturdiness and accuracy of steel products